Moment Connections with Cast-in Anchors
Currently, the principal method used to connect slabs to walls is a proprietary CARES-approved reinforcement continuity system; reinforcing bars are supplied pre-bent in a metal box which is cast-in flush with the face of the wall, upon removal of the formwork the bars are straightened and tied to the slab reinforcement.
Alternatively, but not so common, is the use of reinforcement couplers provided with a suitable embedded anchorage length in accordance with BS8110 or EC2; in this case the couplers are cast into the wall face and once the formwork is removed, threaded continuation bars screwed in to the couplers make the connection with the slab. This method has advantages over reinforcement continuity systems where the slab starter bars must be bent out and straightened by site workers, however it can add to rebar congestion in the wall.
Instead of couplers with rebar anchorage, another option is the use of cast-in headed anchors which also accept threaded continuation bars; however this method has been limited by the length of the anchors necessary to achieve the characteristic strength of the reinforcement. It is this latter option which will be examined in this article, giving an insight into a project to determine the pull out capacity of anchors used in moment connections.
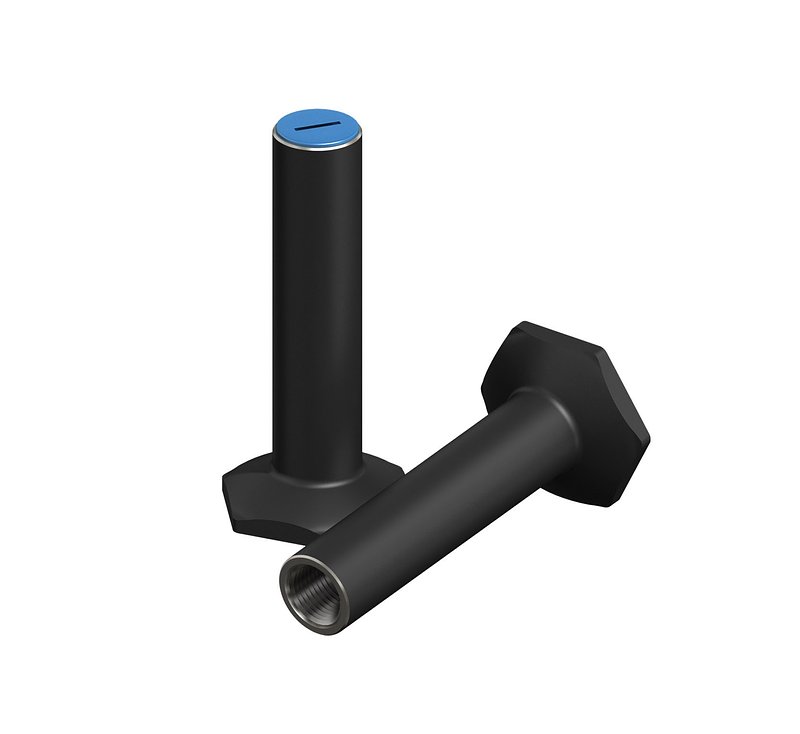
Project Scope
Design procedures are well established for direct tension pull out strength of cast-in anchors. The existing procedures do not however cover guidance for cast-in anchors with moment resisting connections. This article will outline a project completed by Ancon, in conjunction with Heriot Watt University, School of the Built Environment, Edinburgh, to determine the enhancement in concrete cone pull out capacity with moment connections, thus enabling the design of shorter anchor lengths which also achieve the characteristic strength of the reinforcement.
The test results demonstrate that there is useful enhancement in concrete cone capacity when the pull out failure surface is modified by the presence of an adjacent compression force forming part of the moment couple, see below.
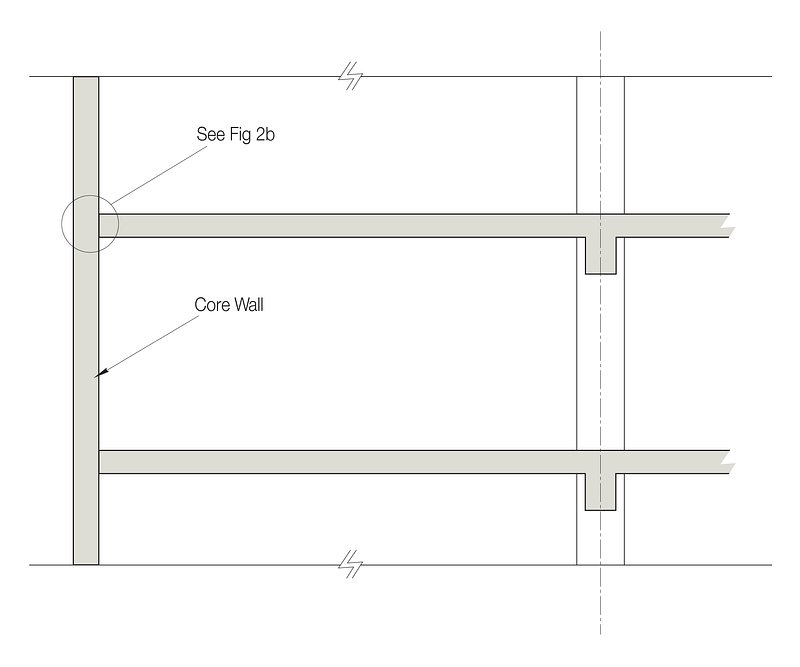
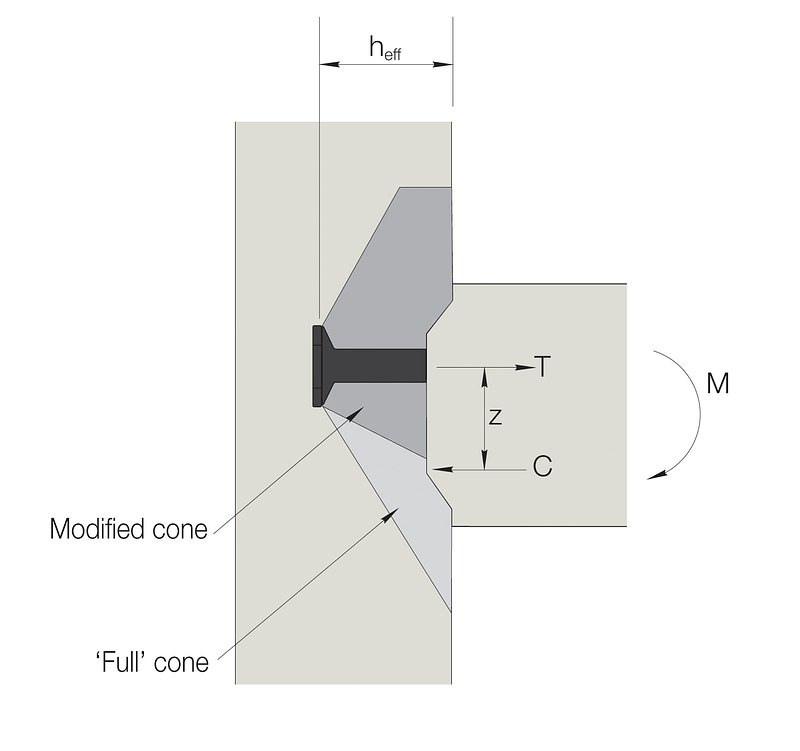
Where an isolated headed anchor is subjected solely to axial tension T, the failure surface is assumed to take the form of a cone or pyramid with a projected surface dimension equal to three times the embedment depth of the anchors. However, when a compression force C acts parallel to and a short distance away from the tension force, the shape of the failure cone is modified as indicated in Fig.2b; the CEB Design Guide for Fastenings in Concrete makes reference of this beneficial effect, but does not quantify its magnitude. Earlier tests by Ancon observed that the outer diameter of the failure cone at the surface of the concrete test block was approximately six times the embedment depth of anchor. It is therefore not unreasonable to assume that the enhancement in the tensile value of the cone capacity would increase with the proximity of the compression force C, but any enhancement would reduce towards zero by the time the compression force was a distance of three times the embedment depth heff from the tension anchor.
Anchorage Lengths
The introduction of BS EN 1992-1-1:2004 (EC2) has introduced some changes to lap lengths and the contribution of hooks and bends to anchorage, the subject is covered in detail in a paper published in the Structural Engineer.
This area is briefly examined here, as the lap lengths required by EC2 may in some instances preclude the use of the commonly used reinforcement continuity systems; the leg lengths for the bent starter bars become longer and thus impractical for use with pre-bent continuity box systems.
The tables below provide data on the anchor bar lengths required for 12mm, 16mm and 20mm bars with ‘good’ and ‘poor’ bond conditions in C32/40 concrete. It can be seen that dimension ‘c’ becomes large in ‘poor’ bond conditions. It is not however envisaged that ‘poor’ conditions will be common in walls; this could, however be different for the top steel slab starter bars and thus require longer lap lengths. It is under such circumstances that the use of cast-in anchors may prove a practical solution.
Anchor bar length required EC2 – Table 5.24, bond conditions, good, C32/40
Rebar dia mm | Wall Width (W) mm | Coupler (l) mm | Dim. a mm | Dim. b mm | Dim. c mm | Required Anchorage |
---|---|---|---|---|---|---|
12 | 200 | 32 | 175 | 143 | 244 | 34d |
16 | 200 | 40 | 175 | 135 | 381 | 34d |
20 | 250 | 48 | 225 | 177 | 528 | 34d |
Anchor bar length required EC2 – Table 5.24, bond conditions, poor, C32/40
Rebar dia mm | Wall Width (W) mm | Coupler (l) mm | Dim. a mm | Dim. b mm | Dim. c mm | Required Anchorage |
---|---|---|---|---|---|---|
12 | 200 | 32 | 175 | 143 | 388 | 46d |
16 | 200 | 40 | 175 | 135 | 573 | 46d |
20 | 250 | 48 | 225 | 177 | 768 | 46d |
Tests
The test arrangement was a cantilever slab projecting from a concrete wall. The tests were arranged to cover slabs 175mm to 300mm deep with a 200mm thick wall, and horizontal anchor spacing 150mm to 300mm. All wall and slab test specimens were 600mm wide. The wall was supported near the top by a triangulated steel frame which in turn was tied to the laboratory strong floor. A spreader beam distributed the applied load across the width of the slab. The loading was applied incrementally, with the development of cracking monitored at each load increment.
The top steel conformed to grade BS4449:2005, grade B500B, 12mm, 16mm and 20mm diameter bars and in all cases the bottom steel was 12mm diameter. The wall steel consisted 16mm diameter vertical bars in both faces with 12mm horizontal reinforcement at 200mm centres. The horizontal bars were ‘U’ shaped and it is considered that they would not contribute to the pull out resistance; earlier tests on individual anchors had also demonstrated this fact.
The walls were cast first, complete with KS Anchors, and the slabs concreted when the walls were approximately 7 days old. The timing of the tests was adjusted to obtain wall compressive strengths as close as practicable to the target compressive cube strength of 40MPa. The test arrangement is shown below.
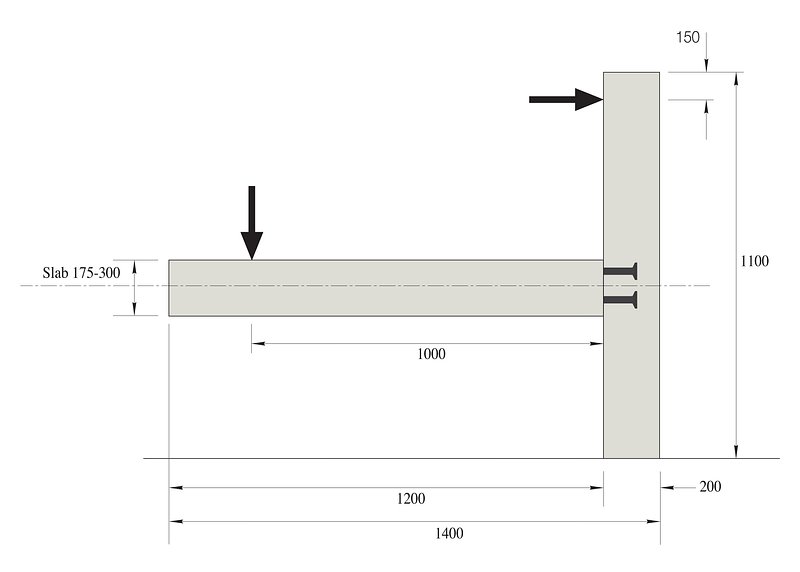
Results
Two principal crack patterns at failure were evident (see below). Both started with formation of diagonal cracking in the wall within the depth of the slab. In both cases the major cracks ran up the wall from the wall/slab joint, the first shows a concrete cone failure mode, whilst the second represents a reinforcement yielding failure.
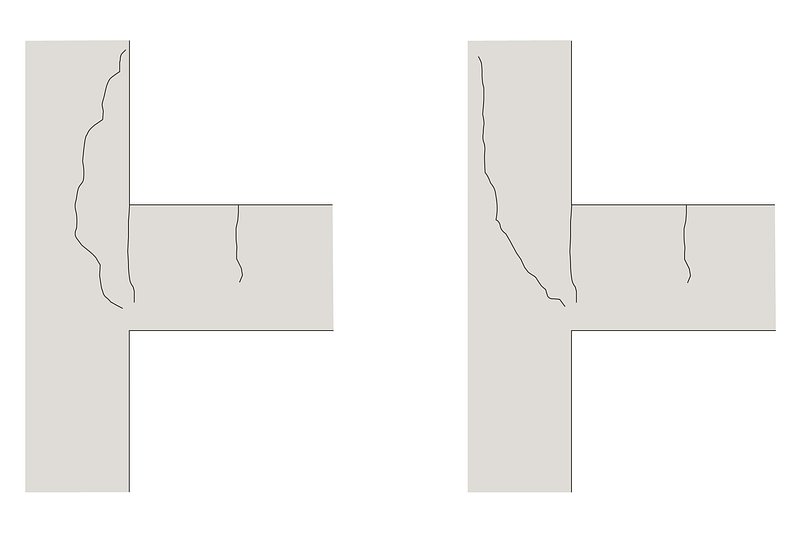
Analysis of the test results demonstrated that significant enhancement of the concrete pull out load is obtained as ratio of ‘heff/d’ increases, where heff is the anchor embedment depth and ‘d’ is the effective depth of the slab, this can clearly be seen below. For the geometries tested, the horizontal spacing of the anchors was found to have a minor influence on anchor capacity.
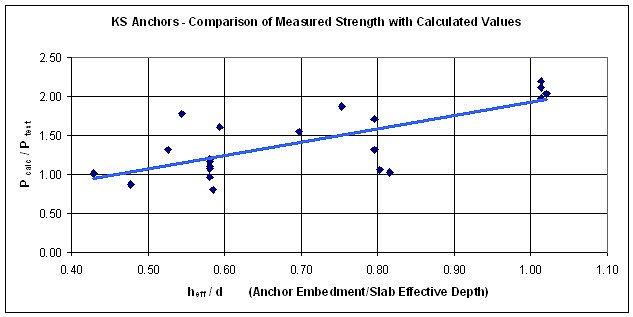
The influence of the distance between the tension and compression chords in the slab is indicated in the graph below.
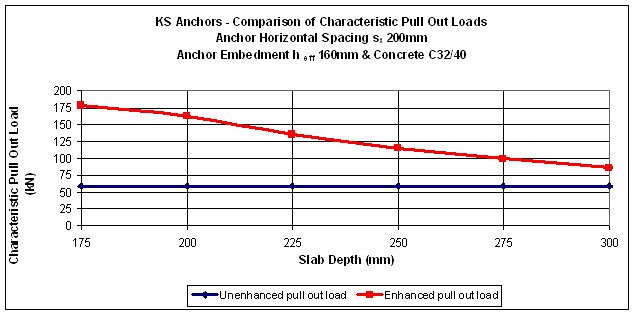
The difference in the characteristic pull out load is shown for KS16 Anchors with an embedment heff of 160mm and horizontal spacing, sx of 200mm, with top and bottom cover to the reinforcement of 25mm. The calculations are based on concrete strength C32/40. The edge distance effect has been omitted in the plot, this would be relatively small, and in most practical applications where more than five anchors are used, it can be neglected when edge reinforcement is provided.
The calculation for unenhanced anchor capacity is independent of slab depth and for a constant horizontal spacing the pull out load will also remain constant. An empirical calculation established from the tests enables the enhanced pull out loads to be determined; the enhancement is greater in thin slabs and gradually migrates towards the unenhanced pull out load as the slabs become deeper and anchor spacing prevails, this was as expected.
The shear in the wall, within the depth of the slab was also examined and design rules established.
Summary
The completed tests demonstrate that significant enhancement in concrete cone capacity when the pull out surface is modified by the presence of an adjacent compression force causing a couple moment. The enhancement is strongly influenced by the ratio of the embedment depth of the anchor to the effective depth of the slab, heff/d.
Design procedures for moment resisting connections using Ancon KS Anchors have been derived, the procedures being compatible with EC2 and the CEB Design guide for fastenings in concrete. Ancon intends to progress towards a standard range of anchors which will enable the designer to specify Ancon KS Anchors and be assured that the concrete tensile design resistance will achieve a strength equal to or greater than the reinforcement characteristic stress value of 500MPa, and the detail will have adequate shear resistance.
The use of these anchors will avoid re-bending and straightening of bars on site and thus reduce misuse. In addition, starter bars greater than 16mm diameter will be possible, although sufficient wall thickness will be required to accommodate the anchors.
John Fallon, Ancon Ltd
Latest News
New White Paper: ‘Bringing Clarity to Masonry Support Systems and Fire Protection Cavity Barriers’
Our latest white paper, authored by our team of industry experts, aims to raise awareness of the interaction between cavity barriers and masonry support systems, and provide clarity for building professionals involved in the design and detailing of such systems.
Leviat Partners with BDA on Educational Brick Works Series 2025
We are thrilled to collaborate on the Brick Development Association’s (BDA) Brick Works Series and contribute to the ongoing conversation about the incredible versatility of clay brick and masonry support solutions.