Precast Connections using Grout Sleeve Coupler Systems
Use of offsite manufacturing for multi-storey concrete frames is increasing in the UK. This trend has necessitated the development of new construction methodologies, particularly in the field of primary structural connections between precast concrete elements.
In this article, Hervé Poveda of Ancon reviews the conventional technology applicable to such connections and provides an insight into new proprietary systems enabling faster, safer and more efficient assemblies.
This article first appeared in CONCRETE magazine, Vol 52, published by The Concrete Society, February 2018.
Spiral Tubing Void Formers
Traditionally, steel spiral tubing, typically 80mm diameter, has been used as a void former within precast concrete elements. Reinforcing bars protruding from one precast element are introduced within these voids in the adjoining precast element. The voids are then filled using high strength cementitious grout to complete the process.
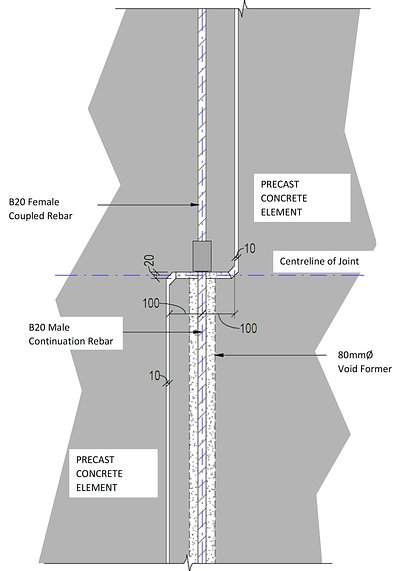
Typical void former construction
Though such connections are relatively simple and cost-effective, they suffer from a number of drawbacks such as:
- Lack of standardised performance data
- Absence of reinforcement continuity
- Necessity to comply with regulatory anchorage lengths
With the introduction of Eurocode 2, the latter point is particularly problematic, as under poor bond conditions this can result in anchorage lengths approaching 60 times nominal bar diameter, with the length of the void former being extended accordingly.
Proprietary Grout Sleeves
To overcome issues associated with void formers, proprietary grout sleeves have been available for a number of years.
Such grout sleeves are usually manufactured from cast iron or cast steel. The sleeves are screwed onto the threaded ends of reinforcing bars, and the projecting bars from the adjoining precast element are grouted into the sleeves to complete the connections. The system has sufficient tolerance to ensure that precast elements are correctly aligned. Cementitious grouts used with grout sleeves typically have a compressive strength in excess of 69MPa after 28 days.
Early proprietary grout sleeve systems were developed for use with lower grade reinforcing bars, typically having a characteristic strength of 460MPa.
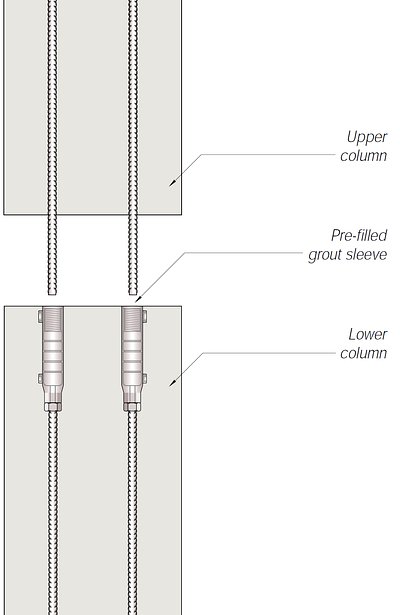
Precast column connection with the grout sleeves in the lower column. The grout sleeves are prefilled with cementitious grout before the connection is made.
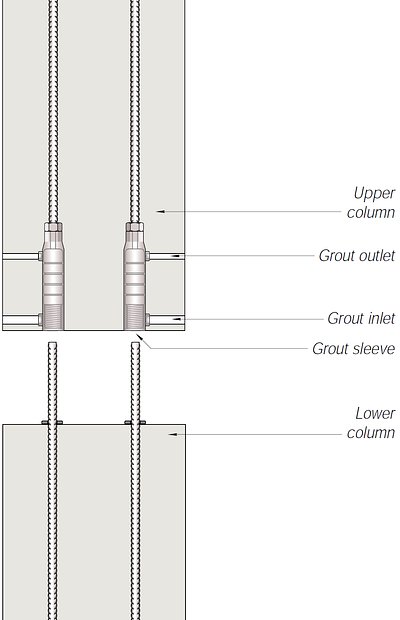
Precast column connection with the grout sleeves in the upper column. The cementitious grout is pumped into the lower inlet of each sleeve after the upper column is in place. Sealing rings on the lower bars retain the grout in the sleeve.
New Generation High Performance Grout Sleeves
As reinforcing bars with a higher characteristic strength of 500MPa are now in use and performance requirements for mechanical reinforcement splices have become more stringent, it has become necessary to look into new, improved grout sleeve systems, focusing on two specific aspects:
- The design of the sleeve itself i.e. optimisation of product features and geometry, material specification and production methodology
- The properties of the cementitious grout
Full Grout Sleeves and Half Grout Sleeves
To broaden the field of application, two product types are now available: Full Grout Sleeves and Half Grout Sleeves.
The reinforcing bars used with a Full Grout Sleeve require no bar end preparation, such as threading, and are simply inserted to meet at the nominal centre point of the sleeve.
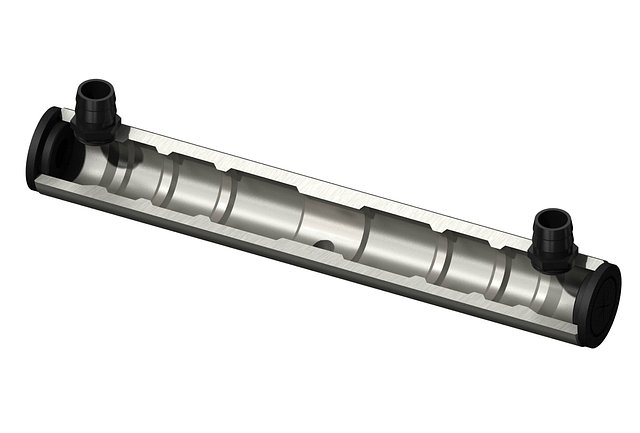
Ancon HM Full Grout Sleeve
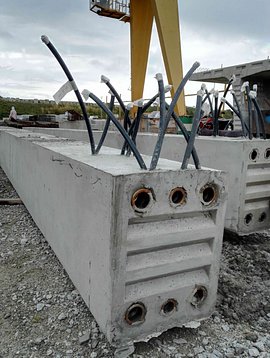
Ancon HM Full Grout Sleeve in Precast Element
Half Grout Sleeves feature a threaded insert to accept a pre-threaded bar, while the other end is open to accommodate an unthreaded continuation bar. The thread profile of the insert can be machined to suit a variety of systems including tapered threads, parallel oversized cut threads or parallel oversized rolled threads, depending on the type of application and level of performance required.
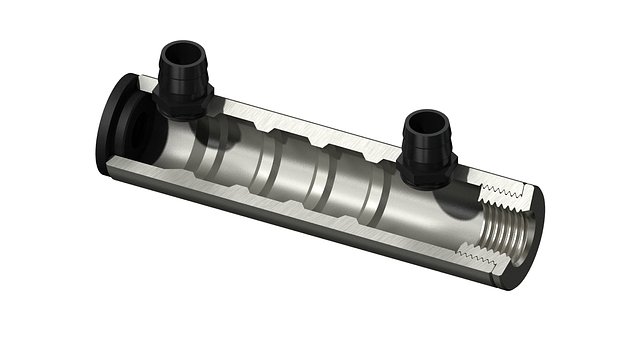
Ancon HM Half Grout Sleeve
Both Full Grout and Half Grout Sleeves are manufactured using fine-point machined high strength seamless steel tubes, in order to guarantee an optimum level of performance. They are ideal for even highly sensitive applications such as earthquake-resistant and fatigue-resistant structures.
High Strength Shrink-Compensated Cementitious Grout
The development of high performance grouts has progressed significantly in recent years. The new generation of Ancon Grout Sleeves has therefore been tested in conjunction with the most advanced pre-bagged grouts on the market, which have a minimum compressive strength of 80MPa after 3 days and in excess of 100MPa after 28 days.
Sleeve optimisation and the use of high performance grouts guarantee the highest level of performance, characterised by:
- A bar break remote failure mode after a three-day cure time regardless of bar size
- Permanent set values in the range 0.019 – 0.067mm
(these values must be limited typically to a figure of 0.1mm after one load cycle (up to 65% of characteristic bar strength and return to zero load) for durability reasons, to ensure that crack width under load is no more than 0.3mm to prevent water penetration and corrosion of reinforcement) - Ductility [Agt %] in excess of 7.5%
Tests undertaken show compliance with performance specifications, including ISO 15835 and BS 8597, and demonstrate suitability for conventional structures as well as for applications where durability and system integrity are of prime importance, such as the nuclear field.
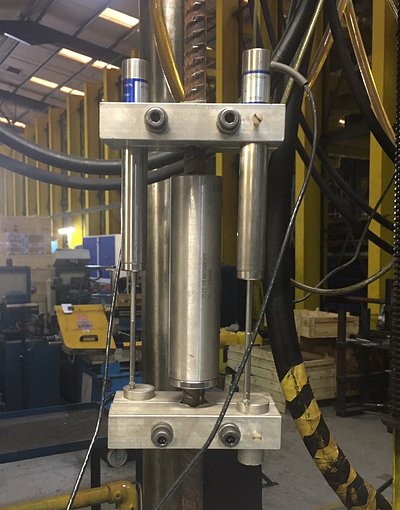
Ancon HM Half Grout Sleeve under test
Concluding remarks
Precast concrete connection systems have evolved from simple void formers, enabling the insertion and grouting of reinforcing bars, to fully optimised grout sleeve systems that, when used with the latest types of high strength cementitious grouts, can guarantee a fully ductile mode of failure and the highest degree of durability.
Use of interchangeable threaded inserts in the case of Half Grout Sleeves enables compatibility with a range of common coupler thread profiles such as tapered threads, parallel oversized cut threads and parallel oversized rolled threads.
Tests undertaken have shown compliance with the most recent national and international Standards, and demonstrate that the latest generation of grout sleeve systems are suitable for the most demanding structural applications, including nuclear work.
This development is particularly important at a time where offsite and modular construction techniques are increasingly under consideration.
Contact Ancon for further information.
Latest News
New EPDs for Key Product Ranges
Environmental Product Declarations (EPDs) covering two key masonry support and restraint solutions from our trusted Ancon product range are now available. Architects, engineers and contractors can now access these verified documents which provide clear, comparable data on the full lifecycle impact of our products.
New Ancon Staifix Packaging: Built for strength, designed for clarity
Leviat’s brand refresh of its established Ancon Staifix range introduces bold, fresh, and sustainable new packaging – designed for visibility, strength, and reliability.
0 comments
Please leave a comment using the form below